Materiales de reparación para pavimentos de concreto
Existen varios tipos de materiales cementantes que se emplean con frecuencia para reparar estructuras de concreto. Entre ellos podrían citarse, además del concreto a base de cemento hidráulico, otros concretos como los elaborados a base de yeso, de fosfato de magnesio, o con altos contenidos de alúmina. El material de reparación más utilizado es el concreto elaborado a base de cemento hidráulico, también conocido como Concreto de Cemento Portland (CCP), que debe cumplir determinados requisitos. Por ejemplo: deben tener resistencias a la compresión mayores a 35 MPa (según lo establece en ASTM C 150: 25 MPa, a 7 días), con relación agua/material cementante (a/c) máxima de 0,42, y contenido total de aire incluido de entre 6 % y 8 %. Si la estructura de concreto reparada exige pronta apertura para ser puesta en servicio –como es el caso generalizado de los pavimentos de concreto es necesario emplear materiales de fraguado rápido o de elevada resistencia inicial, en cuyo caso es común usar aditivos acelerantes. Un cemento o mortero hidráulico de fraguado rápido debe cumplir requisitos tales como el tiempo de fraguado inicial, que deberá ser, como mínimo, de 30 minutos, según lo establece ASTM C403 –Método de prueba estándar para el tiempo de fraguado de mezclas de concreto por resistencia a la penetración. En este caso se requiere que la mezcla tenga trabajabilidad suficiente para permitir la colocación y compactación antes del fraguado inicial. Otros requisitos son la resistencia a la compresión mínima, la contracción y la durabilidad ante ciclos de hielo-deshielo. Respecto a la resistencia mínima, se especifica que debe alcanzar 8,25 MPa a la edad de dos horas. La expansión/contracción se deberá evaluar según ASTM C157 –Método de prueba estándar para cambio de longitud en concreto y mortero de cemento hidráulico endurecido–así como la durabilidad ante los ciclos hielo-deshielo de acuerdo con ASTM C666 –Método de prueba estándar para la resistencia del concreto a ciclos rápidos de hielo y deshielo. Otros requerimientos a tener en cuenta son el uso de productos sin cloruros y la utilización del cemento antes de que expire su vida útil especificada. En muchas ocasiones se tiende a reducir el período de reparación porque los procesos se llevan a cabo en construcciones en operación, lo cual crea alta demanda de materiales de reparación que brinden elevadas resistencias iniciales para diversas aplicaciones; en este caso suelen ser muy utilizados los aditivos superplastificantes.
Reparación de pavimentos de concreto
El caso de la reparación de pavimentos de concreto no es la excepción. Además de los productos elaborados a base de epóxicos, metacrilatos (metil-metacrilato), microsilica, cementos de fosfato de magnesio y cemento base yeso, también los concretos de cemento hidáulico pueden ser una solución eficaz para la reparación de estas estructuras, especialmente cuando se requiere de la sustitución total o parcial del pavimento. En general, el concreto elaborado con cemento hidráulico puede desarrollar, a edad temprana, niveles de resistencia a la compresión mayores a 20 MPa a 3 días, en cuyo caso se pueden usar aditivos químicos acelerantes para mejorar propiedad. Existen tres grupos de acelerantes: los altamente alcalinos, el vidrio de aluminato de calcio finamente molido, y algunos aniones específicos (haluro, nitrato, nitrito, formiato, etc.). Los acelerantes altamente alcalinos actúan aumentando el pH de la fase líquida y aceleran así la hidratación del aluminato tricálcico (C3A).
Si se utilizan silicatos alcalinos, el SiO2 soluble está inmediatamente disponible para reaccionar con el hidróxido de calcio para formar cantidades adicionales de la fase de CSH. Por otra parte, si el vidrio de aluminato de calcio finamente molido se mezcla en el cemento hidráulico, se genera una reacción con el sulfato de calcio presente en el cemento y se forma etringita, lo cual acelera el proceso inicial de fraguado, aunque además reduce la resistencia a la compresión a corto plazo.
También algunos aniones aceleran el proceso de hidratación del silicato tricálcico (C3S), lo que contribuye a desarrollar resistencia a edad temprana al acortarse el tiempo de fraguado, aunque con menor eficacia que cuando se usan aditivos, los cuales tienden, por lo general, a aumentar el pH de la fase líquida.
De hecho, una investigación patrocinada por el Departamento de Transporte del Estado de Oklahoma y por la Administración Federal de Carreteras de Estados Unidos demostró la posibilidad de producir concretos con buen acabado y trabajabilidad para su posible aplicación en la reparación de pavimentos. Con este estudio, los concretos para la reparación de pavimentos mostraron niveles de resistencia a la compresión mayores a 30 MPa a tan solo 6 horas, con el empleo de cemento hidráulico (tipo II según ASTM), así como con aditivos químicos acelerantes, reductores de agua de alto rango e incorporadores de aire; el calor de hidratación en las primeras edades y las características de la contracción por secado también pudieron optimizarse.
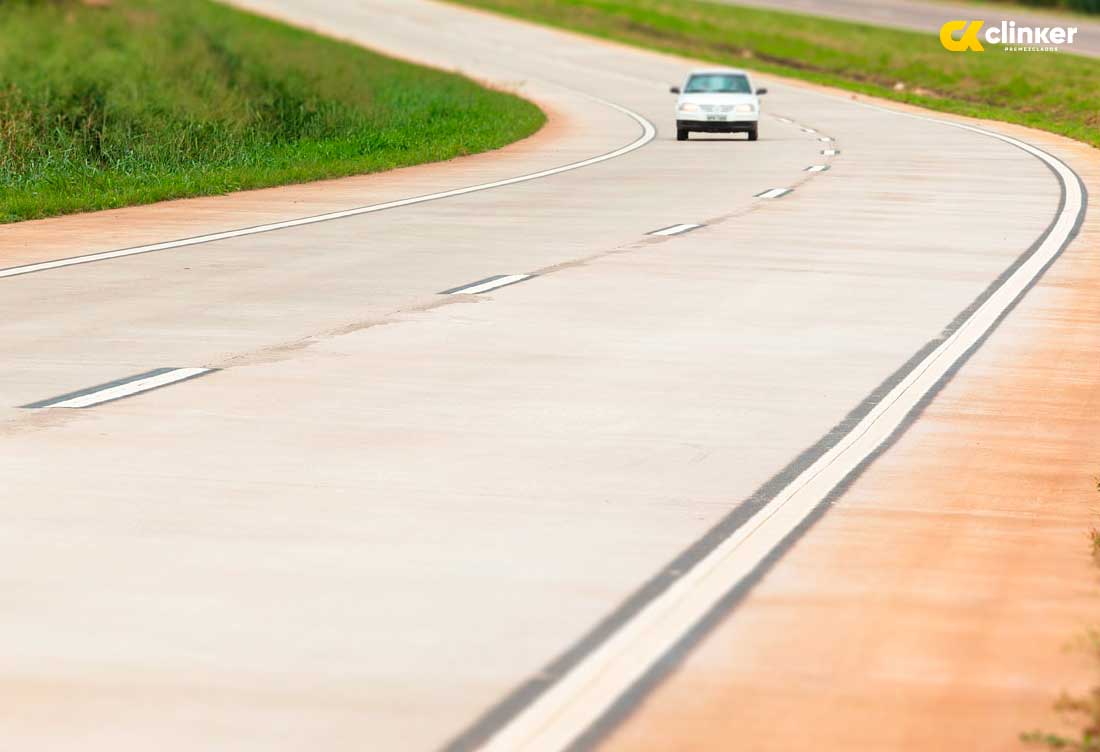
Otros materiales cementicios utilizados en la reparación de pavimentos son los elaborados con cemento de aluminato (o de alta alúmina) y de sulfoaluminato de calcio, y con cemento de fosfato de magnesio. Con el cemento de alta alúmina –cuyo principal constituyente es el aluminato monocálcico– se obtiene resistencia con mayor rapidez que con el cemento hidráulico tradicional. Este material debe utilizarse con relaciones agua / material cementante menores a 0,40 a fin de atenuar los problemas asociados a la estabilidad intrínseca de la mezcla. Existen reportes del uso de este material en la reparación de pavimentos de los aeropuertos de Heathrow en Londres, de Glasgow en Escocia, el Charles de Gaulle en París, y de Stuttgart en Alemania. El cemento de sulfoaluminato de calcio, cuyo principal componente es el sulfoaluminato de calcio anhidro, es un compuesto muy reactivo que, combinado con el sulfato de calcio, forma etringita; con ello se garantizan rápido fraguado y elevada resistencia a edad temprana. Alternativamente, con la presencia de cal libre será más lenta la formación de etringita, pero más expansiva. Este fenómeno constituye la base para obtener cementos expansivos o de contracción compensada. Estos concretos —además de ganar resistencia con relativa rapidez manifiestan una buena adherencia y muy escasa contracción luego de colocados. Se utilizan como concreto refractario. Sin embargo, con el tiempo pueden perder resistencia debido a sus propias reacciones químicas.
En el cemento de fosfato de magnesio, compuesto por óxido de magnesio y por un fosfato ácido soluble en agua, la velocidad inicial de la reacción a temperatura ambiente es rápida y está asociada a la liberación de calor. Un mortero elaborado con este cemento puede tener más de 50 MPa, y con él se puede obtener una excelente unión a sustratos de concreto ya existentes; de ahí que su aplicación es recomendable para reparar estructuras de concreto en que resulta trascendental la preparación de los sustratos. Este material puede utilizarse para reparar superficies impermeables que exigen que el producto se adhiera a superficies limpias y secas. Existen diversos estudios en torno a los materiales de reparación rápida en concreto a base de fosfatos.
Estos materiales suelen elaborarse a partir de la mezcla de óxido de magnesio y polvo de fosfato diádico de amonio (NH4 H2 PO4 ) con bórax. Algunas investigaciones han evaluado la composición química de referencia, así como las propiedades mecánicas del material de reparación resultante; han encontrado que es de buena adherencia y compatibilidad con el concreto, tiene baja contracción y muestra aceptable resistencia a ciclos de congelación y deshielo.
Otros materiales cementicios utilizados en la repa- ración de pavimentos son los elaborados con cemento de aluminato (o de alta alúmina) y de sulfoaluminato de calcio, y con cemento de fosfato de magnesio. Con el cemento de alta alúmina –cuyo principal consti- tuyente es el aluminato monocálcico– se obtiene resistencia con mayor rapidez que con el cemento hidráulico tradicional. Este material debe utilizarse con relaciones agua / material cementante menores a 0,40 a fin de atenuar los problemas asociados a la estabilidad intrínseca de la mezcla. Existen reportes del uso de este material en la reparación de pavimen- tos de los aeropuertos de Heathrow en Londres, de Glasgow en Escocia, el Charles de Gaulle en París, y de Stuttgart en Alemania. El cemento de sulfoaluminato de calcio, cuyo principal componente es el sulfoaluminato de calcio anhidro, es un compuesto muy reactivo que, combinado con el sulfato de calcio, forma etringita; con ello se garantizan rápido fraguado y elevada resistencia a edad temprana. Alternativamente, con la presencia de cal libre será más lenta la formación de etringita, pero más expansiva. Este fenómeno constituye la base para obtener cementos expansi- vos o de contracción compensada. Estos concretos —además de ganar resistencia con relativa rapidez– manifiestan una buena adherencia y muy escasa contracción luego de colocados. Se utilizan como concreto refractario. Sin embargo, con el tiempo pueden perder resistencia debido a sus propias reacciones químicas.
En el cemento de fosfato de magnesio, compuesto por óxido de magnesio y por un fosfato ácido soluble en agua, la velocidad inicial de la reacción a temperatura ambiente es rápida y está asociada a la liberación de calor. Un mortero elaborado con este cemento puede tener más de 50 MPa, y con él se puede obtener una excelente unión a sustratos de concreto ya existentes; de ahí que su aplicación es recomendable para reparar estructuras de concreto en que resulta trascendental la preparación de los sustratos. Este material puede utilizarse para reparar superficies impermeables que exigen que el producto se adhiera a superficies limpias y secas. Existen diversos estudios en torno a los materiales de reparación rápida en concreto a base de fosfatos.
Estos materiales suelen elaborarse a partir de la mezcla de óxido de magnesio y polvo de fosfato diádico de amonio (NH4 H2 PO4 ) con bórax. Algunas investigaciones han evaluado la composición química de referencia, así como las propiedades mecánicas del material de reparación resultante; han encontrado que es de buena adherencia y compatibilidad con el concreto, tiene baja contracción y muestra aceptable resistencia a ciclos de congelación y deshielo.
Deja un comentario